Gefran Temperature and Process Controls
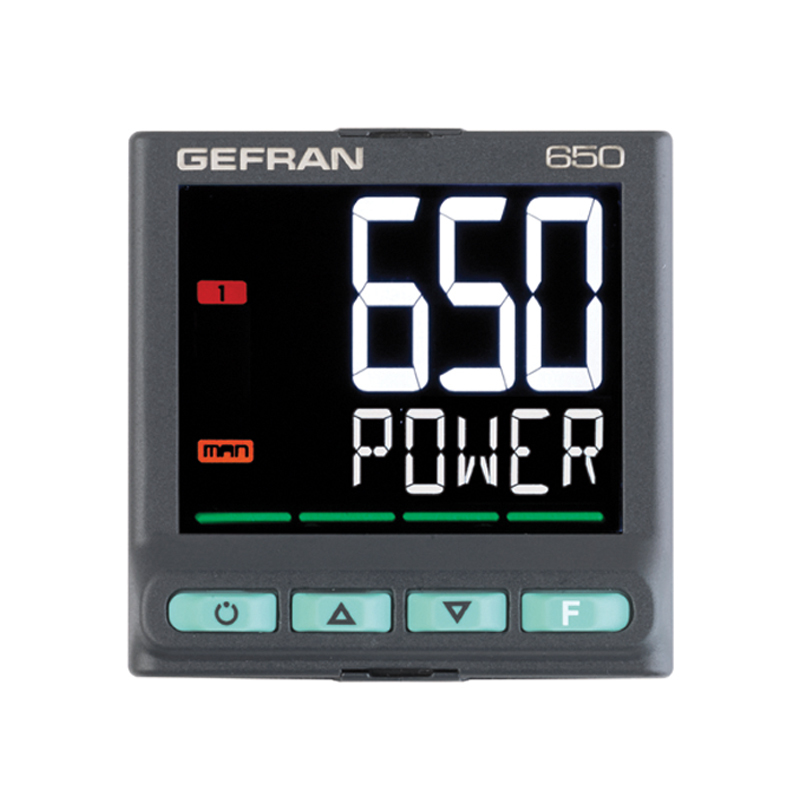
650 PID Controller, 1/16 DIN
Operator interface
Large LCD display with customization of colors assigned to PV and SV display, of color of plastic faceplate, and of logo.
Scrolling alphameric display of 25 messages (32 letters each), completely configurable and savable, in three languages.
Thanks to language selection and clear scrolling messages for diagnostics, alarms, and process state, the controller speaks the user’s language.
Easy Configuration
Guided configuration for manual-free programming, with a few essential parameters and on-line help messages.
Ability to clone configuration among controllers, even with power off and in the field, thanks to a mini portable configurator with Zapper battery.
Extended configuration, creation of work recipes, and firmware updates via PC and GF_eXpress software, even without powering the controllers.
Thanks to the smart configurator function, you obtain the required parameter recipe by answering a few simple questions.
Local configuration and operation with only four keys assigned to LEDs that serve as feedback for the pressed key and as guide to specify appropriate steps.
The initial parameters can always be reset, both from the keypad and from the GF_eXpress Software tool.
Diagnostics, preventive maintenance and energy monitor
Complete diagnostics for broken or incorrectly connected probe, total or partial load break, out of range variables, and control loop faults.
Thanks to the switching count and to the settable alarm thresholds, you can program preventive maintenance to replace worn actuators.
An internal energy counter with alarm for abnormal variations totalizes energy consumptions and costs for constant control
Function block applications
Sixteen AND, OR, timer function blocks let you create customizable logic sequences for complete and flexible machine control.
The controller’s hardware resources are exploited completely, without any need for external devices such as timers and small PLCs
Tuning
Advanced tuning algorithms ensure stable and accurate control even with critical or very rapid thermal systems, engaging automatically when necessary.
Timer
Three types of timers let you set delay times before activating the control, hold times on the setpoint value, and timed changes of programmed setpoints.
Setpoint Programmer
Models with twelve ramp and hold steps, groupable in four programs, with enable inputs and event outputs, are available for applications with setpoint profiles.
On-board configuration and graphic configuration with GF_eXpress.
Valve Positioner
Models to control motorized valves, without feedback.
Valve position is calculated and shown on the display.
General characteristics
The controller is completely software configurable without accessing the internal electronics.
The universal main input accepts thermocouple sensors, resistance thermometers, and linears.
The controller can be replaced at any time simply by removing the faceplate, without any additional procedures
Description
- Operator interface with large LCD Display, customizable, with choice of colors
- Scrolling diagnostics messages, configurable, in the selected language
- Easy, guided configuration, copy/paste parameters even with power off
- Preventive maintenance with energy counters (kWh) and load switching
- 16 function block applications
- Timer, setpoint and algorithm programmer for controlling motorized valves
- Advanced tuning of control parameters
- Different password levels
- Universal input configurable for thermocouples, resistance thermometers, linear inputs
- Remote setpoint input
- Relay, logic, isolated analog outputs
- Up to two CT inputs for interrupted load diagnostics
- RS485 serial communication in Modbus RTU
- Removable faceplate for immediate replacement
- Sampling time 60ms
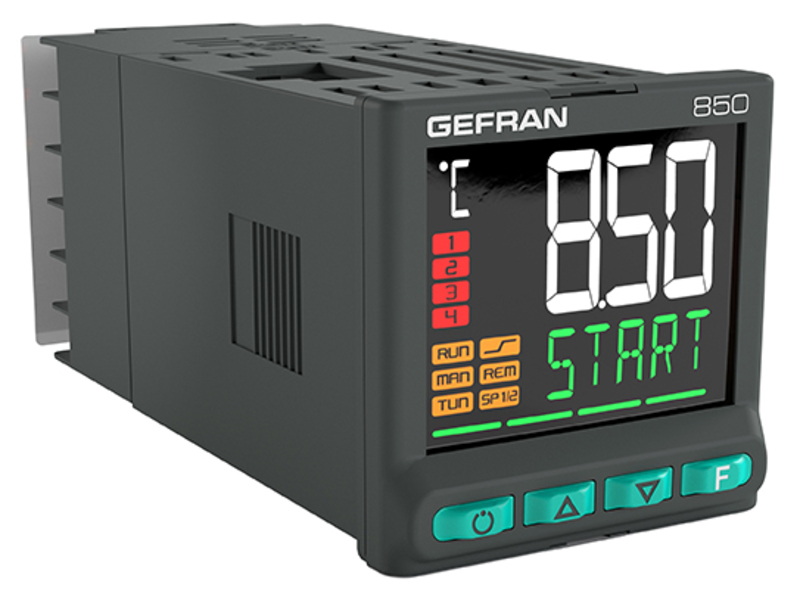
850 Double Loop PID Controller, 1/16 DIN
Overview
Operator interface
Large LCD display with customization of plastic front panel color and logo.
Graphic display of power, output current or valve position.
Scrolling alphameric display of 25 messages (32 letters each), completely configurable and savable, in three languages.
Thanks to language selection and clear scrolling messages for diagnostics, alarms, and process state, the controller speaks the user’s language.
Control
Double loop, three configurable universal inputs for thermocouples, resistance thermometers, linear inputs. Aerospace and Automotive applications AMS2750/CQI-9 conformant.
Easy configuration
Guided configuration for manual-free programming, with a few essential parameters and on-line help messages.
Ability to clone configuration among controllers, even with power off and in the field, thanks to a mini portable configurator with Zapper battery.
Extended configuration, creation of work recipes, and firmware updates via PC and GF_eXpress software, even without powering the controllers.
Thanks to the smart configurator function, you obtain the required parameter recipe by answering a few simple questions.
Local configuration and operation with only four keys assigned to LEDs that serve as feedback for the pressed key and as guide to specify appropriate steps.
The initial parameters can always be reset, both from the keypad and from the GF_eXpress Software tool.
Diagnostics, preventive maintenance and energy monitor
Complete diagnostics for broken or incorrectly connected probe, total or partial load break, out of range variables, and control loop faults.
Thanks to the switching count and to the settable alarm thresholds, you can program preventive maintenance to replace worn actuators.
An internal energy counter with alarm for abnormal variations totalizes energy consumptions and costs for constant control.
Function block applications 32 AND, OR, Timer Function Blocks let you create customizable logic sequences for complete and flexible machine control.
The controller’s hardware resources are exploited completely, without any need for external devices such as timers and small PLCs.
There are 8 math function blocks to process analog variables and add/subtract/multiply/ divide, calculate average, root, logarithms and control functions in cascade, and ratio check.
Options are available with 8 digital inputs/outputs and 8 additional relay outputs to be managed via function blocks with state signals via dedicated LEDs on the LCD display.
Tuning
Advanced tuning algorithms ensure stable and accurate control even with critical or very rapid thermal systems, engaging automatically when necessary.
Timer
Three types of timers let you set delay times before activating the control, hold times on the setpoint value, and timed changes of programmed setpoints.
Setpoint programmer
Models with 128 steps (each step consisting of a ramp and a hold), groupable in a maximum of 16 programs, are available for applications with setpoint profiles.
Enable inputs, event outputs, and messages to display can be assigned to each step.
Double programmer with synchronous and asynchronous base times for activating two setpoint profiles (even separate) assigned to the two loops.
On-board configuration and graphic configuration with GF_eXpress.
Valve positioner
Models to control motorized valves, with or without feedback.
The position is calculated for floating valves.
For valves with potentiometer via auxiliary input you can control and display the position.
Connectivity
Modbus RTU master/slave, Modbus TCP slave and Bridge Modbus RTU/TCP.
Embedded Webserver interface for easy and quick remote service.
General characteristics
The controller is completely software configurable without accessing the internal electronics.
The universal main input accepts thermocouple sensors, resistance thermometers, and linears.
The controller can be replaced at any time simply by removing the faceplate, without any additional procedures.
Description
- Operator interface with large LCD display and three configurable bar graph
- Scrolling diagnostics messages, configurable, in the selected language
- Easy, guided configuration, copy/ paste parameters even with power off
- Preventive maintenance with energy counters (kWh) and load switching
- 32 function block applications
- 8 math application blocks
- Timer, setpoint and algorithm programmer for controlling motorized valves
- Advanced tuning of control parameters
- Different password levels
- 3 universal inputs configurable for thermocouples, resistance thermometers, linear inputs
- AMS2750/CQI-9 conformant
- 2 PID control loop
- 2 setpoint programmers (128 steps in 16 programs)
- Relay, logic, isolated analog outputs
- Up to two CT inputs for interrupted load diagnostics
- RS485 serial communication in Modbus RTU
- Removable faceplate for immediate replacement
- Sampling time 60 ms
- Modbus RTU master/slave
- Modbus TCP slave
- Bridge Modbus RTU/TCP
- Webserver
- Weekly clock (RTC)
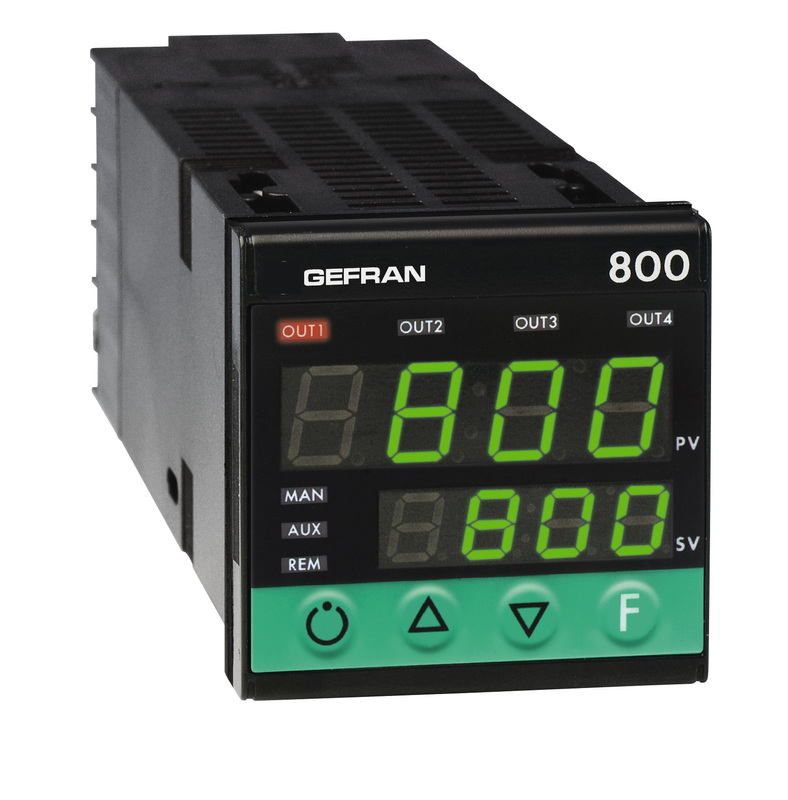
800 PID Controller, 1/16 DIN
Overview
Microprocessor controller, format 48x48 (1/16 DIN) manufactured using SMT.
The instrument provides a complete operator interface, protected by a Lexan membrane that ensures level IP65 faceplate protection.
It has 4 keys, two green LED displays, each with 4 digits, 4 red indicating LED's for the 4 logic or relay outputs, and a further 3 LED's that are programmable to indicate the various operational states of the instrument.
The main input for the process variable is universal and provides the possibility to connect many types of input sensor: thermocouple type J, K, R, S, T, B, E, N, Ni-Ni18Mo, L; resistance thermometer Pt100 3-wires; thermistor PTC; linear inputs 0-50mV, 10-50mV, 2-10V, 0-10V, 0-20mA, 4-20mA, and potentiometer, all with the possibility of custom linearisation that can be defined using the faceplate keys.
It is possible to activate correction of the input using a linear function defined by way of two points on it.
The type of input is selected from the faceplate keys and no external shunts or adapter are required.
A second auxiliary isolated analogue input is available, which can also be configured for a linear input (0-10V, 2-10V, 0-20mA / 4-20mA), for remote setpoint, potentiometer or current transformer.
The auxiliary input function is completely configurable, including the possibility of a custom linearization. It is possible to configure the 2 available isolated digital inputs for selection of up to 4 local setpoints; start, stop and reset of internal timer; Auto/Man, Loc/Rem functions; alarms memory reset; input hold function.
The instrument can have up to 4 relay (3A/250V) or logic (12Vdc, 20mA) outputs and up to 2 islolated analogue outputs in voltage or current.
The function of each output is completely configurable by faceplate.
The available functions include: control output, alarm output, timer, digital input repetition, retransmission of process value, setpoints, deviation, alarm setpoint or value read from digital communication.
A further isolated output (10 or 24Vdc, 30mA max.) is available for powering external transmitters or potentiometers.
The serial communication interface RS485 (RS232C compatible) makes it possible to read or modify any parameter and to govern the instrument online (local/remote manual/automatic commutation, internal timer control, direct control of outputs).
Protocols available: MODBUS RTU and CENCAL (Gefran).
The optional serial communications can be Current Loop, RS232 or RS485, while the protocol can be selected between Gefran (Cencal) and Modbus.
Using these it is possible to write to any of the instrument parameters.
All the programming procedures of the instrument are facilitated by the grouping of the parameters in function blocks (CFG for the control parameters, Inp for the inputs, Out for the outputs, etc.) and by the possibility of selecting a simplified menu for entering the most frequently used parameters.
To simplify the configuration even further, a programming kit is available for PC, which includes a menu driven configuration program for Windows and the necessary cable to connect the instrument (see data sheet cod. 80021).
Description
- Universal input configurable from the faceplate
- Accuracy 0,2% f.s.
- Two control outputs: relay, logic or analogue with Heat/Cool function
- 3 configurable alarms
- 2 analogue outputs
- 2 digital inputs with configurable function
- Auxiliary input for C.T. or remote setpoint
- Heater Break or shortcircuit probe alarm
- Self-tuning, Soft-start, Auto-tuning, Man/Auto, Bumpless, Setpoint, Locale/Remoto
- Function multiset, rampa di set, timer
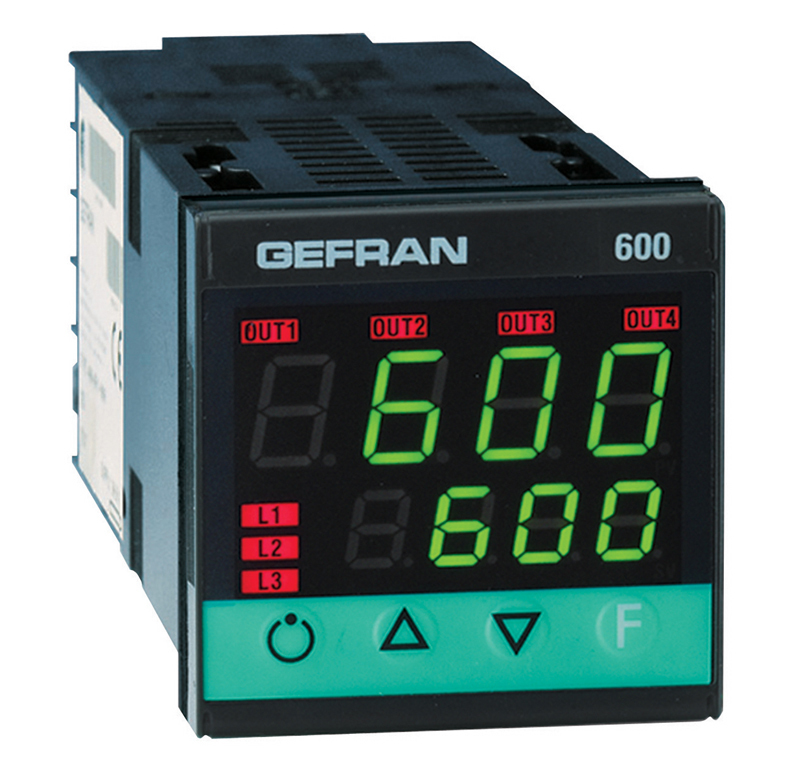
600 PID Controller, 1/16 DIN
Overview
Microprocessor controller, format 48x48 (1/16 DIN) manufactured using SMT.
Provides a complete operator interface protected by a Lexan membrane that ensures level IP65 faceplate protection.
It has 4 keys, two green LED displays, each with 4 digits, 4 red signal LED's for the 4 logic or relay outputs, and 3 other programmable LED's to signal the various operational states of the instrument.
The main input for process variable is universal, and many types of signals can be connected: thermocouples, resistance thermometers, thermistors, normalized linear inputs, all with possibility of custom linearization using the faceplate keys.
The type of input is selected from the faceplate keys; no external shunts are required.
A second auxiliary analog input from the current transformer is also available.
With the isolated digital input you can select: one of the two presettable setpoints, select Manual-Automatic mode, reset the alarms memory, or enable the hold function.
The instrument can have up to 4 outputs: relay (3A, 250V) or logic (12Vdc, 20mA).
An analog output in voltage or current is also available.
The function of each output is freely configurable from the faceplate keys.
In addition to control and alarm outputs, you can have outputs that repeat the state of the digital or retransmission input by process variable, setpoint, drift, alarm limits and values acquired from serial line.
Another isolated output (at 10 or 24Vdc, 30mA max.) is available to power external transmitters.
The serial communication option (available in RS485 standard) allows connection to supervision systems and PLCs with two protocols: GEFRAN CENCAL and MODBUS RTU.
Instrument programming is facilitated by grouping parameters in functional blocks (CFG for control parameters, Inp for inputs, Out for outputs, etc.).
The instrument can also select display parameters based on hardware configuration, automatically masking irrelevant parameters.
The instrument is supplied with an "EASY" configuration with just a few parameters (only those for the model ordered and essential for controller operation).
In this way, you just have to set the setpoint and alarm, and launch selftuning from the button. The 600 does all the rest.
A PC programming kit is available for even simpler configuration, composed of a cable and a guided program for Windows environment (see data sheet code 80020).
Description
- Universal input configurable from faceplate
- Accuracy better than 0.2% f.s. under nominal conditions
- Control output: relay, logic, Triac or continuous
- Hot/cold function with selection of cooling fluid
- 3 alarms with completely configurable function
- Analog retransmission output
- Isolated digital input with configurable function
- Auxiliary input for CT (TA) (50mAac)
- Heater break or probe short-circuit alarm
- Self-tuning, Auto-tuning, Soft-start, bumpless Man/Auto function
- Double set, set ramp, timed output function
- Optically isolated RS485 serial line.
- Protocol: GEFRAN CENCAL or MODBUS RTU
- Self-diagnosis
- Rapid configuration from PC with GF_eXpress packet
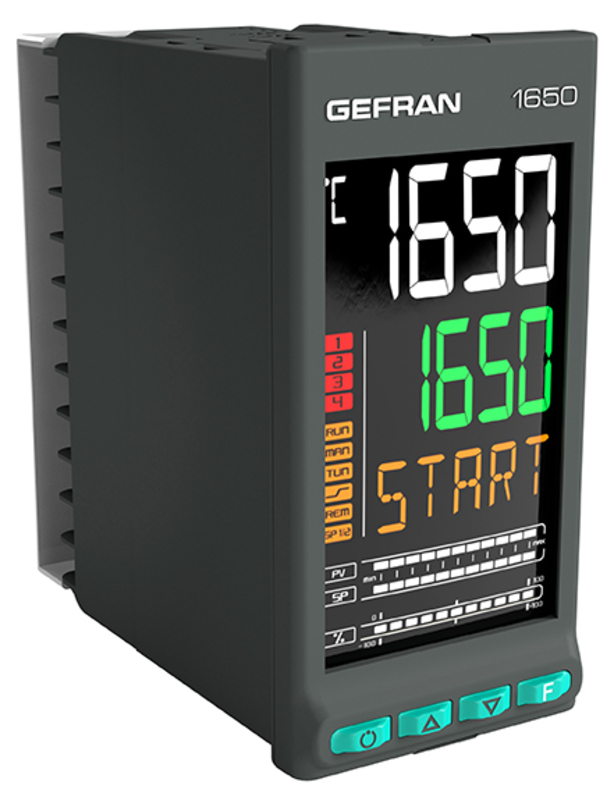
1650 Double Loop PID Controller, 1/8 DIN
Overview
Operator interface
Large LCD display with customization of plastic front panel color and logo.
Graphic display of power, output current or valve position.
Scrolling alphameric display of 25 messages (32 letters each), completely configurable and savable, in three languages.
Thanks to language selection and clear scrolling messages for diagnostics, alarms, and process state, the controller speaks the user’s language.
Control
Double loop, three configurable universal inputs for thermocouples, resistance thermometers, linear inputs. Aerospace and Automotive applications AMS2750/CQI-9 conformant.
Second input can be configured as remote setpoint of single loop.
Easy configuration
Guided configuration for manual-free programming, with a few essential parameters and on-line help messages.
Ability to clone configuration among controllers, even with power off and in the field, thanks to a mini portable configurator with Zapper battery.
Extended configuration, creation of work recipes, and firmware updates via PC and GF_eXpress software, even without powering the controllers.
Thanks to the smart configurator function, you obtain the required parameter recipe by answering a few simple questions.
Local configuration and operation with only four keys assigned to LEDs that serve as feedback for the pressed key and as guide to specify appropriate steps.
The initial parameters can always be reset, both from the keypad and from the GF_eXpress Software tool.
Diagnostics, preventive maintenance and energy monitor
Complete diagnostics for broken or incorrectly connected probe, total or partial load break, out of range variables, and control loop faults.
Thanks to the switching count and to the settable alarm thresholds, you can program preventive maintenance to replace worn actuators.
An internal energy counter with alarm for abnormal variations totalizes energy consumptions and costs for constant control.
Function block applications 32 AND, OR, Timer Function Blocks let you create customizable logic sequences for complete and flexible machine control.
The controller’s hardware resources are exploited completely, without any need for external devices such as timers and small PLCs.
There are 8 math function blocks to process analog variables and add/subtract/multiply/ divide, calculate average, root, logarithms and control functions in cascade, and ratio check.
Options are available with 8 digital inputs/outputs and 8 additional relay outputs to be managed via function blocks with state signals via dedicated LEDs on the LCD display.
Tuning
Advanced tuning algorithms ensure stable and accurate control even with critical or very rapid thermal systems, engaging automatically when necessary.
Timer
Three types of timers let you set delay times before activating the control, hold times on the setpoint value, and timed changes of programmed setpoints.
Setpoint programmer
Models with 128 steps (each step consisting of a ramp and a hold), groupable in a maximum of 16 programs, are available for applications with setpoint profiles.
Enable inputs, event outputs, and messages to display can be assigned to each step.
Double programmer with synchronous and asynchronous base times for activating two setpoint profiles (even separate) assigned to the two loops.
On-board configuration and graphic configuration with GF_eXpress.
Valve positioner
Models to control motorized valves, with or without feedback.
The position is calculated for floating valves.
For valves with potentiometer via auxiliary input you can control and display the position.
Connectivity
Modbus RTU master/slave, Modbus TCP slave and Bridge Modbus RTU/TCP.
Embedded Webserver interface for easy and quick remote service.
General characteristics
The controller is completely software configurable without accessing the internal electronics.
The universal main input accepts thermocouple sensors, resistance thermometers, and linears.
The controller can be replaced at any time simply by removing the faceplate, without any additional procedures.
Description
- Operator interface with large LCD display and three configurable bar graph
- Scrolling diagnostics messages, configurable, in the selected language
- Easy, guided configuration, copy/ paste parameters even with power off
- Preventive maintenance with energy counters (kWh) and load switching
- 32 function block applications
- 8 math application blocks
- Timer, setpoint and algorithm programmer for controlling motorized valves
- Advanced tuning of control parameters
- Different password levels
- 3 universal inputs configurable for thermocouples, resistance thermometers, linear inputs
- AMS2750/CQI-9 conformant
- 2 PID control loop
- 2 setpoint programmers (128 steps in 16 programs)
- Relay, logic, isolated analog outputs
- Up to two CT inputs for interrupted load diagnostics
- RS485 serial communication in Modbus RTU
- Removable faceplate for immediate replacement
- Sampling time 60 ms
- Modbus RTU master/slave
- Modbus TCP slave
- Bridge Modbus RTU/TCP
- Webserver
- Weekly clock (RTC)
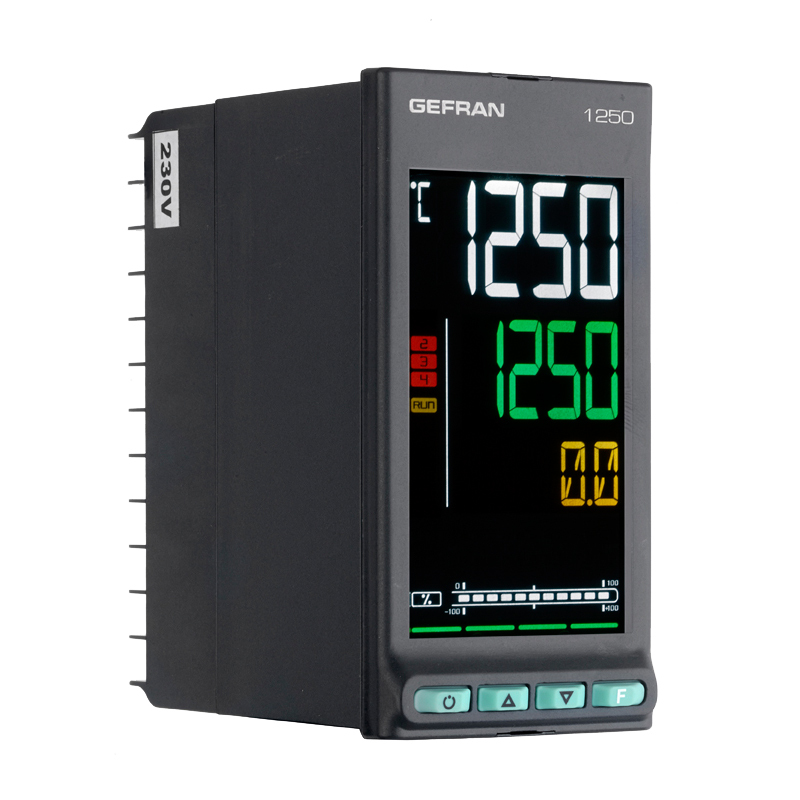
1250 PID Controller, 1/8 DIN
Large LCD display with customization of colors assigned to PV, SV and F display, of color of plastic faceplate, and of logo.
Graphic display of power, output current or valve position.
Scrolling alphameric display of 25 messages (32 letters each), completely configurable and savable, in three languages.
Thanks to language selection and clear scrolling messages for diagnostics, alarms, and process state, the controller speaks the user’s language.
Description
- Operator interface with large LCD Display, customizable, with choice of colors
- Scrolling diagnostics messages, configurable, in the selected language
- Easy, guided configuration, copy/paste parameters even with power off
- Preventive maintenance with energy counters (kWh) and load switching
- 16 function block applications
- Timer, setpoint and algorithm programmer for controlling motorized valves
- Advanced tuning of control parameters
- Different password levels
- Universal input configurable for thermocouples, resistance thermometers, linear inputs
- Remote setpoint input
- Relay, logic, isolated analog outputs
- Up to two CT inputs for interrupted load diagnostics
- RS485 serial communication in Modbus RTU
- Controller assembly removable from the front for quick replacement.
- Accuracy 0.2%, sampling time 60 ms
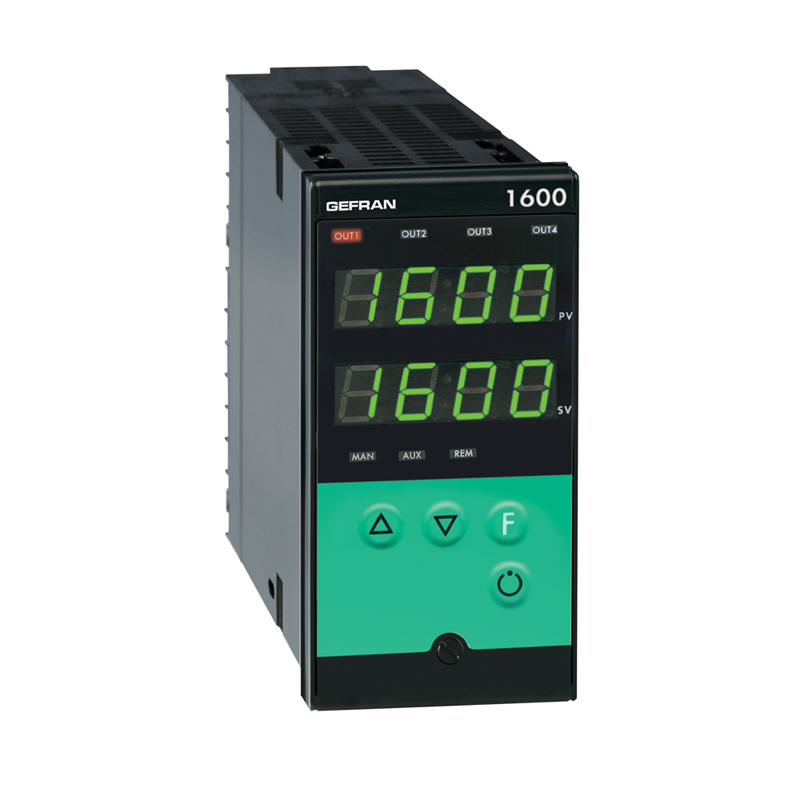
1600 Controller PID, 1/8 DIN
Overview
Microprocessor controller, format 48x48 / 96x96 (1/8 DIN - 1/4 DIN) manufactured using SM Technology.
The instrument provides a complete operator interface, protected by a Lexan membrane that ensures level IP65 faceplate protection.
It has 4 keys, two green LED displays, each with 4 digits, 4 red indicating LED's for the 4 logic or relay outputs, and a further 3 LED's that are programmable to indicate the various operational states of the instrument.
The main input for the process variable is universal and provides the possibility to connect many types of input sensor: thermocouple type J, K, R, S, T, B, E, N, Ni-Ni18Mo, L; resistance thermometer Pt100 3-wires; thermistor PTC; ilinear inputs 0-50mV, 10-50mV, 2-10V, 0-10V, 0-20mA, 4-20mA, and potentiometer, all with the possibility of custom linearisation that can be defined using the faceplate keys.
The type of input is selected from the faceplate keys and no external shunts or adapter are required. A second auxiliary isolated analogue input is available, which can also be configured for a linear input (0-10V, 2-10V, 0-20mA / 4-20mA), for remote setpoint, potentiometer or current transformer.
The auxiliary input function is completely configurable, including the possibility of a custom linearization. It is possible to configure the 2 available isolated digital inputs for selection of up to 4 local setpoints; start, stop and reset of internal timer; Auto/Man, Loc/Rem functions; alarms memory reset; input hold function.
The instrument can have up to 4 relay (3A/250V) or logic (12Vdc, 20mA) outputs and up to 2 islolated analogue outputs in voltage or current.
The function of each output is completely configurable by faceplate.
The available functions include: control output, alarm output, timer, digital input repetition, retransmission of process value, setpoints, deviation, alarm setpoint or value read from digital communication.
The Heat/Cool adjustment offers the possibility of setting the cooling parameters in relation to the type of water, oil or air fluid.
A further isolated output (10 or 24Vdc, 30mA max.) is available for powering external transmitters or potentiometers.
The serial communication interface RS485 (RS232C compatible) makes it possible to read or modify any parameter and to govern the instrument online (local/remote manual/automatic commu-tation, internal timer control, direct control of outputs).
Protocols available: MODBUS RTU and CENCAL (Gefran).
Using these it is possible to write to any of the instrument parameters.
All the programming procedures of the instrument are facilitated by the grouping of the parameters in function blocks (CFG for the control parameters, Inp for the inputs, Out for the outputs, etc) and by the possibility of selecting a simplified menu for entering the most frequently used parameters.
To simplify the configuration even further, a programming kit is available for PC, which includes a menu driven configuration program for Windows and the necessary cable to connect the instrument (see data sheet cod. 80021).
Description
- Universal input configurable from the faceplate
- Acquisition of the input signal every 120msec ; resolution 30000steps
- Two control outputs: relay, logic or analogue with Heat/Cool function
- 3 configurable alarms
- 2 analogue outputs (setpoint retransmission)
- 2 digital inputs with configurable function
- Auxiliary input for C.T. or remote setpoint
- Heater Break or shortcircuit probe alarm
- Self and Auto-tuning, Soft-start, Local/Remote setpoint, Auto/Man
- Function multiset, rampa di set, timer
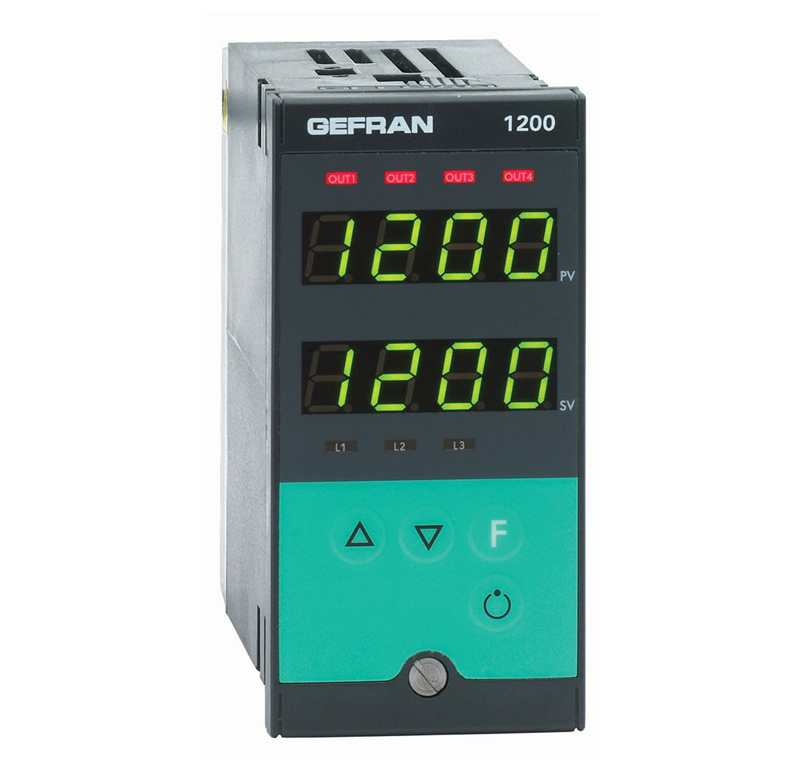
1200 PID Controller, 1/8 DIN
Overview
Microprocessor controllers, 48x96 (1/8DIN) format for 1200 and 96x96 (1/4DIN) format for 1300, built with SMT technology.
Complete operator interface, protected by Lexan membrane to guarantee an IP65 faceplate protection level.
Composed of 4 keys, double 4-digit green LED display, 4 red signal LEDs for the 4 relay/logic outputs and 3 additional LEDs with programmable function to signal the instrument's various function states.
The main input for the variable to be controlled is universal, and allows connection of a wide variety of signals: thermocouples, resistance thermometers, thermistors, normalized linear inputs, all with possibility of custom linearization set from the faceplate. Input type is selected entirely from the faceplate and requires no external adapter shunts/dividers.
A second auxiliary analog input from current transformer is available. You can select one of the two presettable setpoints, select Manual-Automatic mode, reset the alarm memory, or enable the hold function by means of the digital input.
The instrument provides up to 4 outputs: relay (5A, 250VAC/30VDC cosφ = 1) or logic (24V ± 10% (10Vmin a 20mA)).
An analog output in voltage or in current is also available. The functions of each output are freely configurable from the faceplate. In addition to the control and alarm outputs, you can also have outputs that repeat the state of the digital or retransmission input by process variable, setpoint, deviation, alarm trip points and values acquired via serial line.
An additional output (24VDC, 30mA max.) is available to power outside transmitters.
The serial communication option can be in Current Loop or RS485, with MODBUS RTU protocol and maximum speed of 19200 baud (485). The instrument's entire programming procedure is made easier by grouping the parameters in function blocks (CFG for control parameters, Inp for inputs, Out for outputs, etc.).
The instrument can also select the parameters to be displayed based on its hardware configuration, which automatically hides irrelevant parameters.
The instrument is supplied with an "EASY" configuration calling for just a few parameters (only those pertaining to the model ordered and essential to the controller's operation). In this way, you just have to set the setpoint and the alarm, then launch self-tuning with the specific button.
For even simpler configuration, you can use a PC programming kit consisting of a cable and a guided program for Windows environment (see Technical Data code GF_eXpress).
- Universal input configurable from faceplate
- Accuracy better than 0.2% f.s. under nominal conditions
- Control output: relay, logic, Triac or continuous
- Hot/cold function with selection of cooling fluid
- 3 alarms with completely configurable function
- Analog retransmission output
- Up to 2 isolated digital inputs with configurable function
- Isolated digital input with configurable function
- Auxiliary input for CT (TA) (50mAac)
- Heater break or probe short-circuit alarm
- Self-tuning, Auto-tuning, Soft-start, bumpless Man/Auto function
- Double set, set ramp, timed output function
- Optically isolated RS485 serial line. Protocol: GEFRAN MODBUS RTU
- Self-diagnosis
- Rapid configuration from PC with GF eXpress software
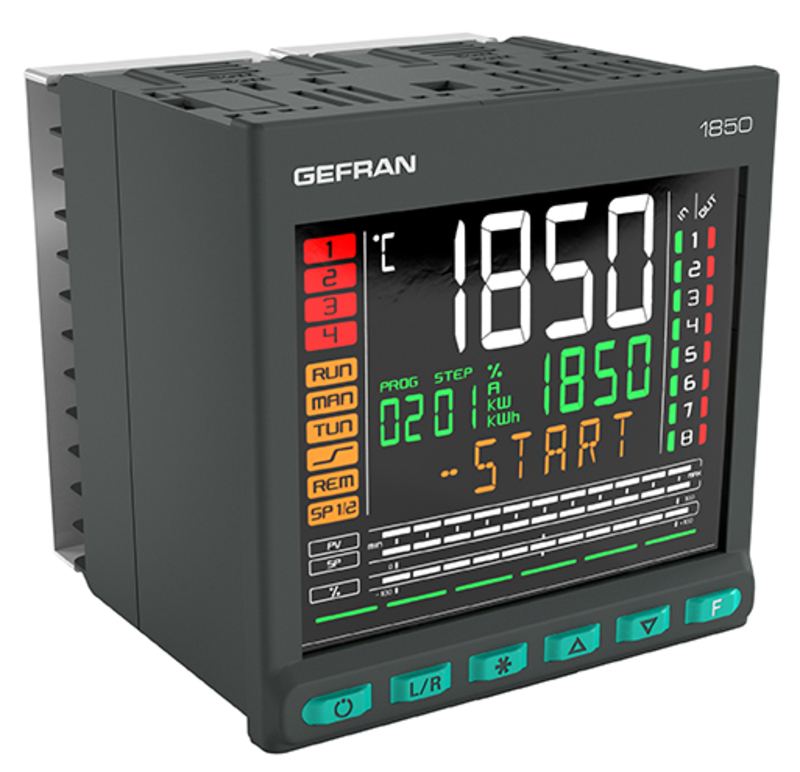
1850 Double Loop PID Controller, 1/4 DIN
Overview
Operator interface
Large LCD display with customization of plastic front panel color and logo.
Graphic display of power, output current or valve position.
Scrolling alphameric display of 25 messages (32 letters each), completely configurable and savable, in three languages.
Thanks to language selection and clear scrolling messages for diagnostics, alarms, and process state, the controller speaks the user’s language.
Control
Double loop, two configurable universal inputs for thermocouples, resistance thermometers, linear inputs. Aerospace and Automotive applications AMS2750/CQI-9 conformant.
Easy configuration
Guided configuration for manual-free programming, with a few essential parameters and on-line help messages.
Ability to clone configuration among controllers, even with power off and in the field, thanks to a mini portable configurator with Zapper battery.
Extended configuration, creation of work recipes, and firmware updates via PC and GF_eXpress software, even without powering the controllers.
Thanks to the smart configurator function, you obtain the required parameter recipe by answering a few simple questions.
Local configuration and operation with only four keys assigned to LEDs that serve as feedback for the pressed key and as guide to specify appropriate steps.
The initial parameters can always be reset, both from the keypad and from the GF_eXpress Software tool.
Diagnostics, preventive maintenance and energy monitor
Complete diagnostics for broken or incorrectly connected probe, total or partial load break, out of range variables, and control loop faults.
Thanks to the switching count and to the settable alarm thresholds, you can program preventive maintenance to replace worn actuators.
An internal energy counter with alarm for abnormal variations totalizes energy consumptions and costs for constant control.
Function block applications 32 AND, OR, Timer Function Blocks let you create customizable logic sequences for complete and flexible machine control.
The controller’s hardware resources are exploited completely, without any need for external devices such as timers and small PLCs.
There are 8 math function blocks to process analog variables and add/subtract/multiply/ divide, calculate average, root, logarithms and control functions in cascade, and ratio check.
Options are available with 8 digital inputs/outputs and 8 additional relay outputs to be managed via function blocks with state signals via dedicated LEDs on the LCD display.
Tuning
Advanced tuning algorithms ensure stable and accurate control even with critical or very rapid thermal systems, engaging automatically when necessary.
Timer
Three types of timers let you set delay times before activating the control, hold times on the setpoint value, and timed changes of programmed setpoints.
Setpoint programmer
Models with 128 steps (each step consisting of a ramp and a hold), groupable in a maximum of 16 programs, are available for applications with setpoint profiles.
Enable inputs, event outputs, and messages to display can be assigned to each step.
Double programmer with synchronous and asynchronous base times for activating two setpoint profiles (even separate) assigned to the two loops.
On-board configuration and graphic configuration with GF_eXpress.
Valve positioner
Models to control motorized valves, with or without feedback.
The position is calculated for floating valves.
For valves with potentiometer via auxiliary input you can control and display the position.
Connectivity
Modbus RTU master/slave, Modbus TCP slave and Bridge Modbus RTU/TCP.
Embedded Webserver interface for easy and quick remote service.
General characteristics
The controller is completely software configurable without accessing the internal electronics.
The universal main input accepts thermocouple sensors, resistance thermometers, and linears.
The controller can be replaced at any time simply by removing the faceplate, without any additional procedures.
Description
- Operator interface with large LCD display and three configurable bar graph
- Scrolling diagnostics messages, configurable, in the selected language
- Easy, guided configuration, copy/ paste parameters even with power off
- Preventive maintenance with energy counters (kWh) and load switching
- 32 function block applications
- 8 math application blocks
- Timer, setpoint and algorithm programmer for controlling motorized valves
- Advanced tuning of control parameters
- Different password levels
- 3 universal inputs configurable for thermocouples, resistance thermometers, linear inputs
- AMS2750/CQI-9 conformant
- 2 PID control loop
- 2 setpoint programmers (128 steps in 16 programs)
- Relay, logic, isolated analog outputs
- Up to two CT inputs for interrupted load diagnostics
- Removable faceplate for immediate replacement
- Sampling time 60 ms
- Modbus RTU master/slave
- Modbus TCP slave
- Bridge Modbus RTU/TCP
- Webserver
- Weekly clock (RTC)
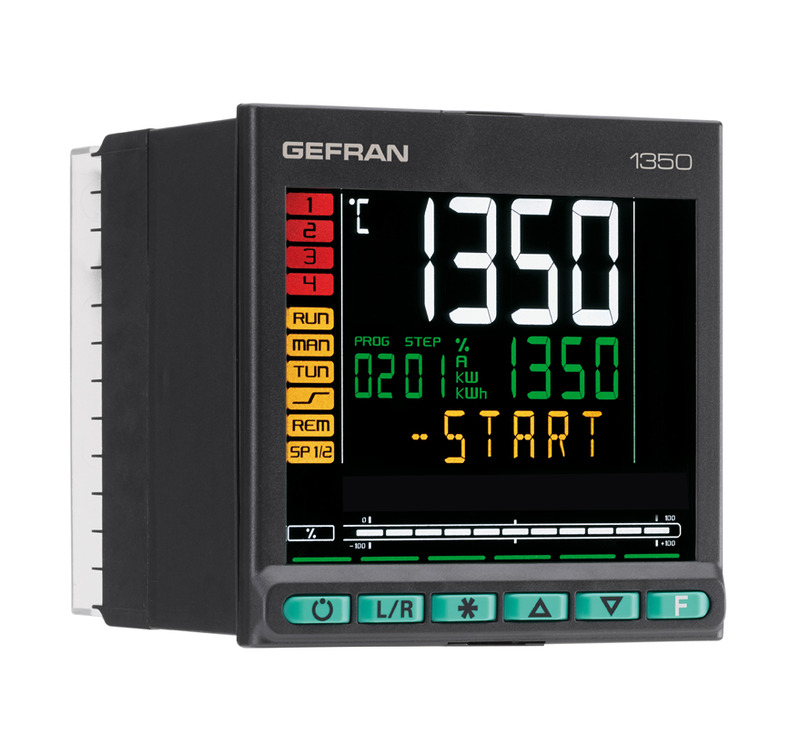
1350 Controller PID, 1/4 DIN
Overview
Operator interface
arge LCD display with customization of colors assigned to PV, SV and F display, of color of plastic faceplate, and of logo.
Graphic display of power, output current or valve position. Scrolling alphameric display of 25 messages (32 letters each), completely configurable and savable, in three languages.
Thanks to language selection and clear scrolling messages for diagnostics, alarms, and process state, the controller speaks the user’s language.
Easy Configuration
Guided configuration for manual-free programming, with a few essential parameters and on-line help messages.
Ability to clone configuration among controllers, even with power off and in the field, thanks to a mini portable configurator with Zapper battery.
Extended configuration, creation of work recipes, and firmware updates via PC and GF_eXpress software, even without powering the controllers.
Thanks to the Smart Configurator function, you obtain the required parameter recipe by answering a few simple questions.
Local configuration and operation with only four keys assigned to LEDs that serve as feedback for the pressed key and as guide to specify appropriate steps.
The initial parameters can always be reset, both from the keypad and from the GF_eXpress software tool.
Diagnostics, Preventive Maintenance, and Energy Monitor
Complete diagnostics for broken or incorrectly connected probe, total or partial load break, out of range variables, and control loop faults.
Thanks to the switching count and to the settable alarm thresholds, you can program preventive maintenance to replace worn actuators.
An internal energy counter with alarm for abnormal variations totalizes energy consumptionsand costs for constant control.
Function block applications
Sixteen AND, OR, Timer Function Blocks let you create customizable logic sequences for complete and flexible machine control.
The controller’s hardware resources are exploited completely, without any need for external devices such as timers and small PLCs.
Tuning
Advanced tuning algorithms ensure stable and accurate control even with critical or very rapid thermal systems, engaging automatically when necessary.
Timer
Three types of timers let you set delay times before activating the control, hold times on the setpoint value, and timed changes of programmed setpoints.
Setpoint Programmer
Models with twelve ramp and hold steps, groupable in four programs, with enable inputs and event outputs, are available for applications with setpoint profiles.
The operator interface provides two additional display dedicated to the permanent display for: Nr. of step and Nr. program.
On-board configuration and graphic configuration with GF_eXpress.
Valve Positioner
Models to control motorized valves, without feedback.
Valve position is calculated and shown on the display.
General characteristics
The controller is completely software configurable without accessing the internal electronics.
The universal main input accepts thermocouple sensors, resistance thermometers, and linears.
The controller can be replaced at any time simply by removing the faceplate, without any additional procedures.
Description
- Operator interface with large LCD Display, customizable, with choice of colors
- Scrolling diagnostics messages, configurable, in the selected language
- Easy, guided configuration, copy/ paste parameters even with power off
- Preventive maintenance with energy counters (kWh) and load switching
- 16 function block applications
- Timer, setpoint and algorithm programmer for controlling motorized valves
- Advanced tuning of control parameters
- Different password levels
- Universal input configurable for thermocouples, resistance thermometers, linear inputs
- Remote setpoint input
- Relay, logic, isolated analog outputs
- Up to two CT inputs for interrupted load diagnostics
- RS485 serial communication in Modbus RTU
- Removable faceplate for immediate replacement
- Accuracy 0.2%, sampling time 60 ms
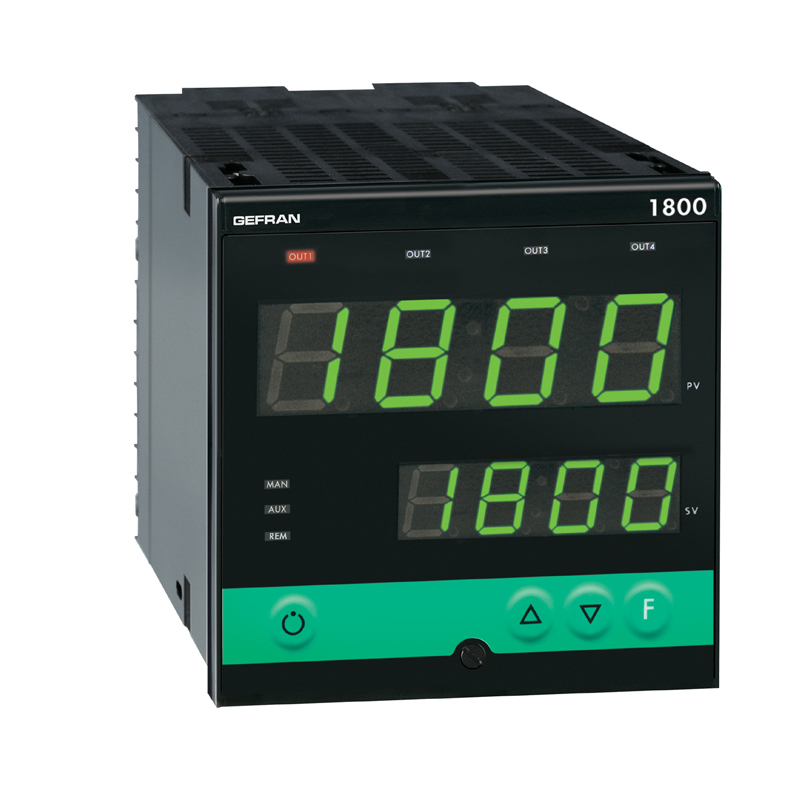
1800 PID Controller, 1/4 DIN
Overview
Microprocessor controller for three-step motorized valves, 48x96 / 96x96 (1/8DIN - 1/4DIN) size.
Manufactured using SM Technology, the instrument provides a complete operator interface, protected by a Lexan membrane that ensures level IP65 faceplate protection.
It has 4 keys, two green LED displays, each with 4 digits, 4 red indicating LED's for the 4 logic or relay outputs, and a further 3 LED's that are programmable to indicate the various operational states of the instrument. 10 led red bargraph indication can be associated with analogue outputs for control, inputs, deviations or valve position.
The main input for the process variable is universal and provides the possibility to connect many types of input sensor: thermocouple, resistance thermometer, thermistor, linear inputs, potentiometer, all with the possibility of custom linearisation that can be defined using the faceplate keys.
The type of input is selected from the faceplate keys and no external shunts or adapter are required.
It is possible to activate correction of the input using a linear function defined by way of two points on it.
A second auxiliary isolated analogue input is available, which can also be configured for a linear input or, potentiometer for valve position feedback.
It is possible to configure the 2 available isolated digital inputs for selection of up to 4 local setpoints; start, stop and reset of internal timer; Auto/Man, Loc/Rem functions; alarms memory reset; input hold function.
This instrument has up to 4 relè (3A, 250V) or logic (12Vdc, 20mA) outputs, 2 of which will be dedicated to the open/close valve functions and up to 2 isolated analogic outputs, in voltage or current.
Every output function is configurable from keypad; available functions are control output (open/close valve); alarm output; timer controlled output; digital input repetition; retransmission of process value, setpoint, deviation, alarm setpoint or value read from digital communication.
A further isolated output (10 or 24Vdc, 30mA max.) is available for powering external transmitters or potentiometers.
The serial communication interface RS485 (RS232C compatible) makes it possible to read or modify any parameter and to govern the instrument online (local/remote manual/automatic commutation, internal timer control, direct control of outputs).
Protocols available: MODBUS RTU and CENCAL (Gefran).
Using these protocols it is possible to write to any of the instrument parameters.
Specific parameters are present for the valves control, i.e. the actuator stroke time, the minimum pulse time, the impulsive intervent treshold, the dead zone; also the control type is configurable with or without potentiometer feedback; with PD or PID algorithm.
All the programming procedures of the instrument are facilitated by the grouping of the parameters in function blocks (CFG for the control parameters, Inp for the inputs, Out for the outputs, etc) and by the possibility of selecting a simplified menu for entering the most frequently used parameters.
The instrument can also select the parameters to display depending on the hardware configuration, automatically hiding those that are not influential.
To simplify the configuration even further, a programming kit is available for PC, which includes a menu driven configuration program for Windows and the necessary cable to connect the instrument (see data sheet cod. 80021).
Description
- Universal input configurable from the faceplate
- Acquisition of the input signal every 120msec ; resolution 30000 steps
- Two control outputs: relay, logic or analogue with Open/Close valve function
- 3 configurable alarms
- 2 analogue outputs (setpoint retransmission)
- 2 digital inputs with configurable function
- Auxiliary input for valve position potentiometer feedback
- Heater Break or shortcircuit probe alarm
- Self and Auto-tuning, Soft-start, Local/Remote setpoint, Auto/Man
- Multiset function, timer set ramp
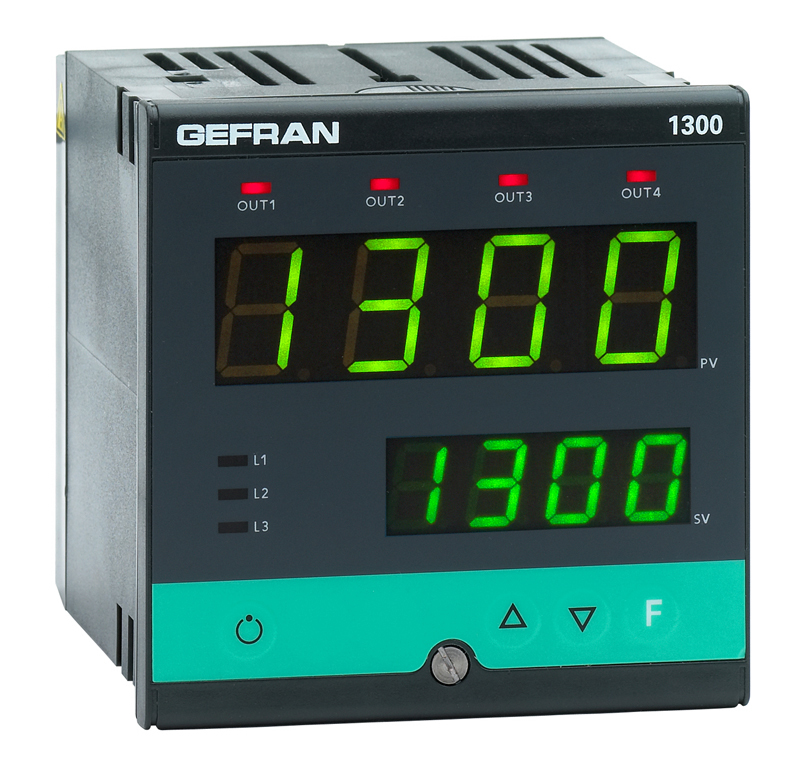
1300 PID Controller, 1/4 DIN
Overview
Microprocessor controllers, 48x96 (1/8DIN) format for 1200 and 96x96 (1/4DIN) format for 1300, built with SMT technology.
Complete operator interface, protected by Lexan membrane to guarantee an IP65 faceplate protection level.
Composed of 4 keys, double 4-digit green LED display, 4 red signal LEDs for the 4 relay/logic outputs and 3 additional LEDs with programmable function to signal the instrument's various function states.
The main input for the variable to be controlled is universal, and allows connection of a wide variety of signals: thermocouples, resistance thermometers, thermistors, normalized linear inputs, all with possibility of custom linearization set from the faceplate. Input type is selected entirely from the faceplate and requires no external adapter shunts/dividers.
A second auxiliary analog input from current transformer is available. You can select one of the two presettable setpoints, select Manual-Automatic mode, reset the alarm memory, or enable the hold function by means of the digital input.
The instrument provides up to 4 outputs: relay (5A, 250VAC/30VDC cosφ = 1) or logic (24V ± 10% (10Vmin a 20mA)).
An analog output in voltage or in current is also available. The functions of each output are freely configurable from the faceplate. In addition to the control and alarm outputs, you can also have outputs that repeat the state of the digital or retransmission input by process variable, setpoint, deviation, alarm trip points and values acquired via serial line.
An additional output (24VDC, 30mA max.) is available to power outside transmitters.
The serial communication option can be in Current Loop or RS485, with MODBUS RTU protocol and maximum speed of 19200 baud (485). The instrument's entire programming procedure is made easier by grouping the parameters in function blocks (CFG for control parameters, Inp for inputs, Out for outputs, etc.).
The instrument can also select the parameters to be displayed based on its hardware configuration, which automatically hides irrelevant parameters.
The instrument is supplied with an "EASY" configuration calling for just a few parameters (only those pertaining to the model ordered and essential to the controller's operation). In this way, you just have to set the setpoint and the alarm, then launch self-tuning with the specific button.
For even simpler configuration, you can use a PC programming kit consisting of a cable and a guided program for Windows environment (see Technical Data code GF_eXpress).
Description
- Universal input configurable from faceplate
- Accuracy better than 0.2% f.s. under nominal conditions
- Control output: relay, logic, Triac or continuous
- Hot/cold function with selection of cooling fluid
- 3 alarms with completely configurable function
- Analog retransmission output
- Up to 2 isolated digital inputs with configurable function
- Isolated digital input with configurable function
- Auxiliary input for CT (TA) (50mAac)
- Heater break or probe short-circuit alarm
- Self-tuning, Auto-tuning, Soft-start, bumpless Man/Auto function
- Double set, set ramp, timed output function
- Optically isolated RS485 serial line. Protocol: GEFRAN MODBUS RTU
- Self-diagnosis
- Rapid configuration from PC with GF eXpress software
Gefran 1300 PDF brochure (missing)
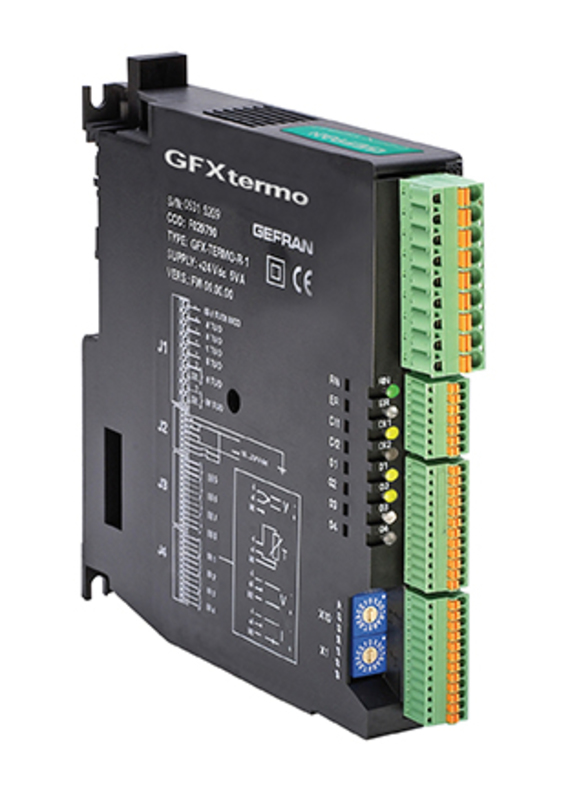
GFXTermo4 PID Controller 4 loops for DIN rail
Overview
GFXTERMO4 is a multi-loop control system that controls four process loops in a completely independent manner. Configuration of I/O resources is very rapid and flexible thanks to a programming tool that guides the user in the selection of parameters. Each control loop has:
- Process input
- Input for external CTs or CT / linear input
- Control output
- Cooling output Other auxiliary I/Os:
- Two digital inputs
- Two relay outputs
The use of two independent serial ports provides efficient communication ability. The two serials are defined as follows:
- “local bus” to create a GFXTERMO4 network and connect it to an operator panel or industrial PC. Uses Modbus RTU protocol and reaches a speed of 115 Kbps.
- “field bus” to integrate with architectures that already use industrial field buses such as: Profibus DP, CANopen, DeviceNet, Modbus RTU, Ethernet Modbus TCP.
The presence of “intelligence” directly on the board lets the user create fully independent and reliable controls. The device installs on the DIN rod or with two M4 screws.
- 4 universal process inputs
- 4 independent hot/cold PIDs
- 4 main outputs
- 4 auxiliary analog inputs
- 4 configurable outputs: relay / logic / TRIAC / continuous
- 2 configurable relay
- 2 digital inputs
- Standard communication port: Modbus RTU
- Optional port for Fieldbus: Profibus DP, CANopen, DeviceNet, Modbus RTU, Ethernet Modbus TCP
- Installs on DIN rod and panel
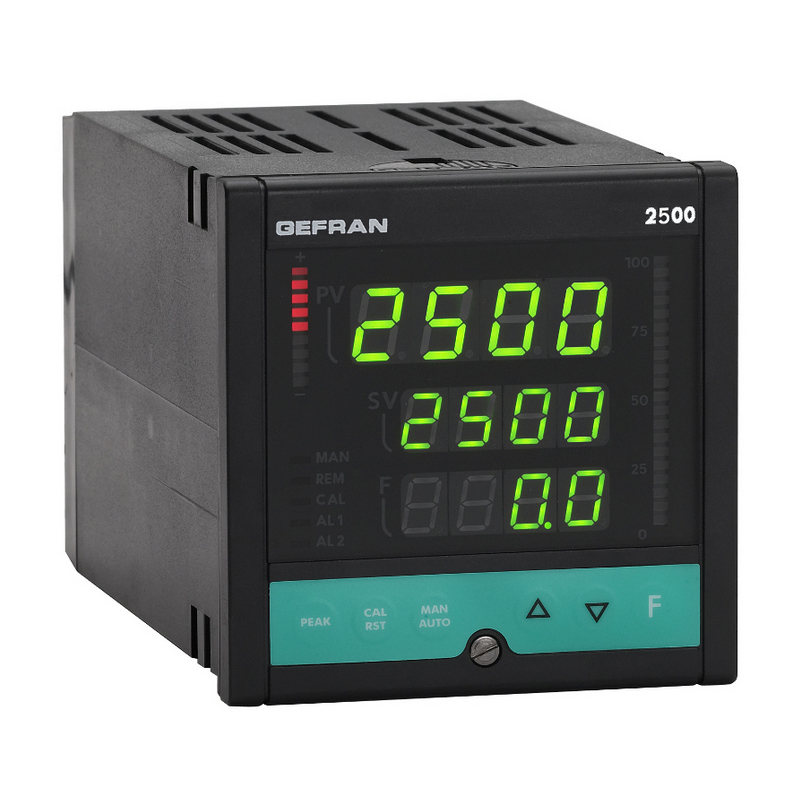
2500 PID Controller Pressure and Force, 1/4 DIN
Overview
Single-loop microprocessor controller, 96 x 96 (1/4 DIN) format, appropriate for processes with high variation speed.
Thanks to its extended functions and configurable hardware and software, it provides high applicative flexibility in systems that control and monitor pressure, force, temperature, and differential pressure, and can acquire up to 4 variables.
It has two main analog inputs, configurable for strain gauge / potentiometer / linear signal / TC / RTD (one of which is optional) and two auxiliary analog inputs for linear signals (for example, remote setpoint functions and line speed reference input).
Two isolated analog outputs (one of which is optional) are available for control.
The operator interface, with IP54 protection level (IP65 with protective cover) is equipped with a 6-key soft-touch keyboard, triple 5-digit display (one of which is 2-color), and two bar graphs with configurable function.
Controls and commands can be sent from the front panel or via 4 digital inputs that can be assigned functions such as reset, calibration, man/auto, loc/rem, hold, raise/lower (motopotentiometer function), parameter set selection, setpoint selection.
The instrument has 4 configurable relay outputs as standard. More extended configurations are available with the following options:
- isolated analog output for retransmission of process, peak, remote set, deviation, alarm setpoint, differential values
- expansion with 4 I/O
- communication interface Modbus RTU
- communication interface Profibus DP (slave)
Controller
Self-adapting PI control or double-action PID (heating/cooling), ratio controller, differential pressure controller, selftuning, continuous or one-shot autotuning, Auto/man, Loc/rem, setpoint gradient, power gradient, dynamic power limits. 8 sets of selectable PID parameters based on setpoint level / PV / deviation or from digital inputs.
Alarms
4 completely configurable alarm setpoints.
Selectable “failsafe” function.
Math functions
The 2500 controller lets you define two distinct math relations between two analog inputs. The results can be freely used as setpoints, alarm setpoints, control output, etc...
Digital communication
The instrument offers an optional RS485 2/4 wire / RS232 serial interface with MODBUS RTU protocol for access to instrument parameters.
Configuration
The programming procedure is facilitated by the menu structure, with various configuration levels for quick and simple data search.
Description
- Double configurable input for strain gauge / potentiometer / linear signal / TC / RTD
- Two auxiliary analog inputs
- Differential measurement
- High precision: 0.1 % f.s. ± 1 digit
- Automatic calibration for 6-wire strain gauge
- Transmitter power supply and strain gauge probe power supply
- PID controls with 8 sets of selectable parameters
- 4 configurable alarms, failsafe function
- Up to 3 isolated analog outputs for control and retransmission
- 4 digital inputs
- 4 relay outputs with configurable function
- Expansion with 4 configurable digital inputs and/or outputs
- Serial communication interface:
- RS485/RS 232 MODBUS RTU protocol (optional)
- Profibus DP Slave (optional) - Front panel with three 5-digit displays and two bar graphs
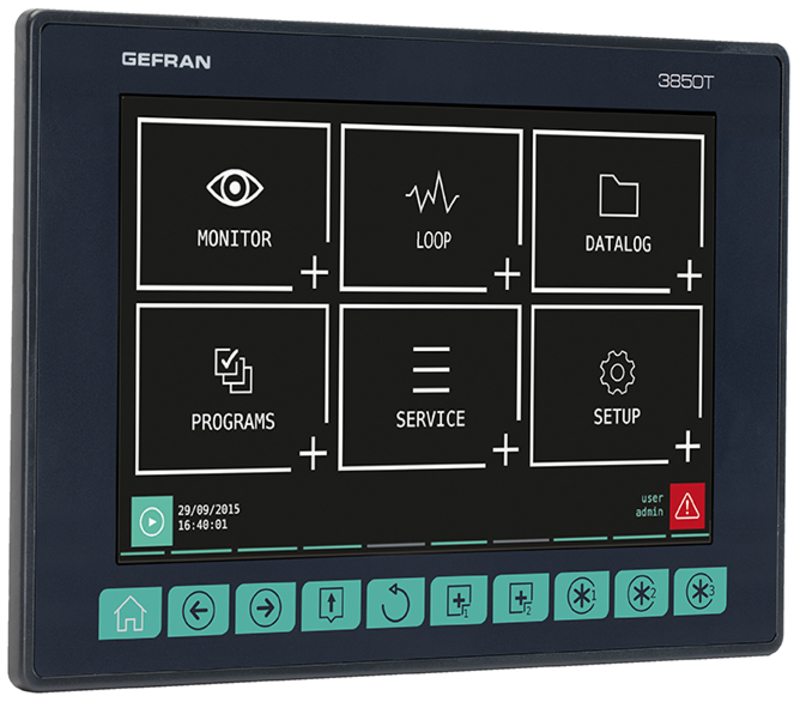
3850T Up to 16 PID loops Controller Programmer and Recorder, 7” graphic touch interface
Overview
3850T Multifunction controller is an all-in-one device. It combines precision PID controllers, secure datalogging, batch reporting, Set Point Programmer (Ramp & Soak), and powerful function block that will allow customized programs with sequence control configurability. The brilliant 7” touch graphic interface makes extremely clear the visualization of process parameters. This technology also provides the capability, from the front of the controller, to be configured without the need of connected PC. The 3850T meets the high accuracy standards of the Aerospace and Automotive Industries with CQI9 and AMS2750.
PID control Loops
3850T can control up to 16 individual PID loops. The flexibility of the 3850T allows the user to utilize a variety of advanced control loop functions. These range from single loop, proportional or motorized valve, ratio control, and cascade control.
The 3850T has multiple tuning methods to give the user precise control over the process. This will ensure stable and accurate temperature control for applications with critical heat demands or fast processes.
Data Logger and Batch report
The Data Logger function, combined with the Real Time Clock stores process data, IN/OUT signals and alarms status in an open file (.CSV format) or encrypted file. The minimum data sampling frequency is 1 second. The batch report option lets you to associate the archived data with a specific batch code reference. The flexibility of the 3850T data format will allow the user to create customized, production and quality reports.
DataLog Utility PC is available for an easy management of all archived data, allows manually or automatically copy, and delete files via an Ethernet network. Data stored on PC can be displayed in trend chart format or a spreadsheet (Excel type) or exported as CSV or PDF files.
Set Point Programmer (Ramp & Soak)
3850T provides an advanced Set Point programmer for the user to create control profiles with ramp, soak, hold, and event In/Out functions for each steps. The multiple process can be setup so that each zone can have synchronize time based or asynchronous times. Guaranteed Soaks, multiple event outputs for auxiliary control can be managed in the Programmer.
GETlogic
Gefran’s GETlogic is an optional programming package on the 3850T controller. GETlogic is part of the GF_Express Tool available for download from Gefran’s website. GETlogic combines logic functions and mathematical functions allowing the user to create customized sequence control with the combined use of advanced process control functions.
The 3850T as an all-in-one device, takes high level process control with math and integrates logic functions. It is now possible with the creation of virtual control channels, with delays, timers, sequence control, logic functions, mathematical functions, along with the precise PID control allowing the user to combine all advanced functions into one 3850T solution.
Custom interface GETview
GETview is also in Gefran’s GF_Express software. GETView allows the user to create graphic customized pages specific to the application. GETview, allows the user to design a dynamic graphic interface that will simplify and make clear the process interactions on the plant floor. Gefran’s includes a graphic symbol library to aid in the development of the customized views. There are easy links to associate the graphic symbols to the controller variables.
GF Express with GETview & GETlogic
GF Express is Gefran’s configuration tool for all of their micro-processor configured products. GETView and GETlogic are parts of the configuration tool for use with the 3850T.
Remote service & Security
The 3850T has several levels of password and security available. These are available for the user to protect the device from unauthorized access or use.
When needed or desired the 3850T will support a remote VNC server service that can by a PC, Tablet, or Smart Phone. This will allow viewing & editing from local or remote locations. The security levels for local access also apply to remote access. The remote service can be used for diagnostics and process views to aid production up time and troubleshooting down equipment.
Description
- Operator interface color touch screen display, 7“
- Up to 16 PID control loops
- Cascade PID control, ratio, and proportional valves
- Advanced PID control loop tuning
- Fully configurable analog signal
- AMS2750 and CQI9 compliance
- Data Log, Trend Charts, and Batch Report with Real Time Clock
- Historical files encrypted or open format (CSV)
- USB for data export and parameter export/import
- Profile programming with ramps and soak
- Up to 250 stored profile programs.
- Synchronous and asynchronous profile programmer
- Configurable logic and math operations (GETlogic)
- Customizable operator graphic interface (GETview)
- 3 password protected user levels
- Energy meter (kWh)
- HMI/SCADA data exchange via Modbus TCP
- Interface language selection
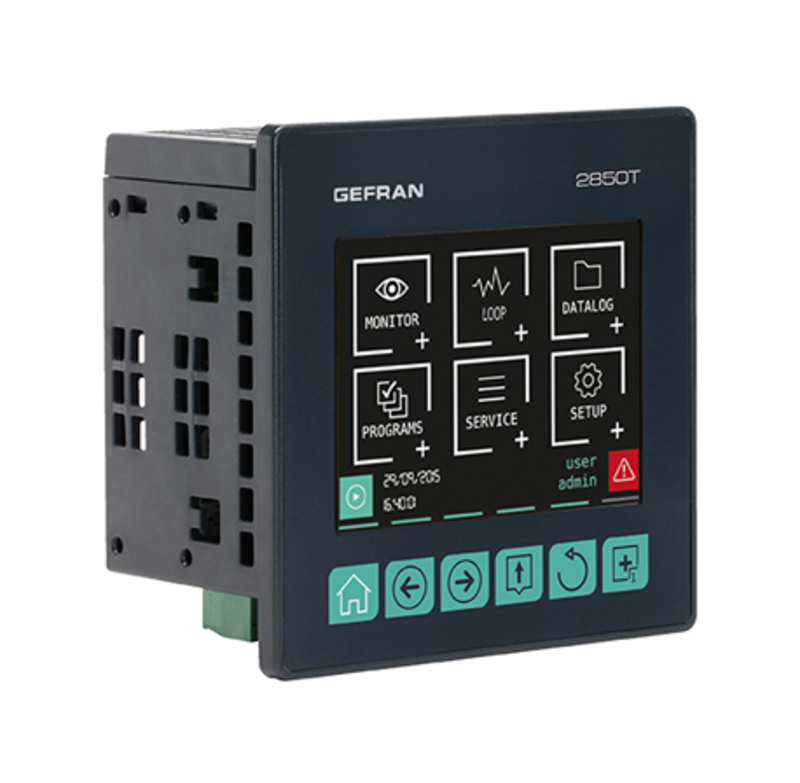
2850T Up to 8 PID loops Controller Programmer and Recorder, 3.5” graphic touch interface
Overview
2850T Multifunction controller is an all-in-one device. It combines precision PID controllers, secure datalogging, batch reporting, Set Point Programmer (Ramp & Soak), and powerful function block that will allow customized programs with sequence control configurability. The brilliant 3.5” touch graphic interface makes extremely clear the visualization of process parameters. This technology also provides the capability, from the front of the controller, to be configured without the need of connected PC. The 2850T meets the high accuracy standards of the Aerospace and Automotive Industries with CQI9 and AMS2750.
PID control Loops
2850T can control up to 8 individual PID loops. The flexibility of the 2850T allows the user to utilize a variety of advanced control loop functions. These range from single loop, proportional or motorized valve, ratio control, and cascade control.
The 2850T has multiple tuning methods to give the user precise control over the process. This will ensure stable and accurate temperature control for applications with critical heat demands or fast processes.
Data Logger and Batch report
The Data Logger function, combined with the Real Time Clock stores process data, IN/OUT signals and alarms status in an open file (.CSV format) or encrypted file. The minimum data sampling frequency is 1 second. The batch report option lets you to associate the archived data with a specific batch code reference. The flexibility of the 2850T data format will allow the user to create customized, production and quality reports.
DataLog Utility PC is available for an easy management of all archived data, allows manually or automatically copy, and delete files via an Ethernet network. Data stored on PC can be displayed in trend chart format or a spreadsheet (Excel type) or exported as CSV or PDF files.
Set Point Programmer (Ramp & Soak)
2850T provides an advanced Set Point programmer for the user to create control profiles with ramp, soak, hold, and event In/Out functions for each steps. The multiple process can be setup so that each zone can have synchronize time based or asynchronous times. Guaranteed Soaks, multiple event outputs for auxiliary control can be managed in the Programmer.
GETlogic
Gefran’s GETlogic is an optional programming package on the 2850T controller. GETlogic is part of the GF_Express Tool available for download from Gefran’s website. GETlogic combines logic functions and mathematical functions allowing the user to create customized sequence control with the combined use of advanced process control functions.
The 2850T as an all-in-one device, takes high level process control with math and integrates logic functions. It is now possible with the creation of virtual control channels, with delays, timers, sequence control, logic functions, mathematical functions, along with the precise PID control allowing the user to combine all advanced functions into one 2850T solution.
Custom interface GETview
GETview is also in Gefran’s GF_Express software. GETView allows the user to create graphic customized pages specific to the application. GETview, allows the user to design a dynamic graphic interface that will simplify and make clear the process interactions on the plant floor. Gefran’s includes a graphic symbol library to aid in the development of the customized views. There are easy links to associate the graphic symbols to the controller variables.
GF Express with GETview & GETlogic
GF Express is Gefran’s configuration tool for all of their micro-processor configured products. GETView and GETlogic are parts of the configuration tool for use with the 2850T.
Remote service & Security
The 2850T has several levels of password and security available. These are available for the user to protect the device from unauthorized access or use.
When needed or desired the 2850T will support a remote VNC server service that can by a PC, Tablet, or Smart Phone. This will allow viewing & editing from local or remote locations. The security levels for local access also apply to remote access. The remote service can be used for diagnostics and process views to aid production up time and troubleshooting down equipment.
Description
- Operator interface color touch screen display, 3,5“
- Up to 8 PID control loops
- Cascade PID control, ratio, and proportional valves
- Advanced PID control loop tuning
- Fully configurable analog signal
- AMS2750 and CQI9 compliance
- Data Log, Trend Charts, and Batch Report with Real Time Clock
- Historical files encrypted or open format (CSV)
- USB for data export and parameter export/import
- Profile programming with ramps and soak
- Up to 250 stored profile programs.
- Synchronous and asynchronous profile programmer
- Configurable logic and math operations (GETlogic)
- Customizable operator graphic interface (GETview)
- 3 password protected user levels
- Energy meter (kWh)
- HMI/SCADA data exchange via Modbus TCP
- Interface language selection
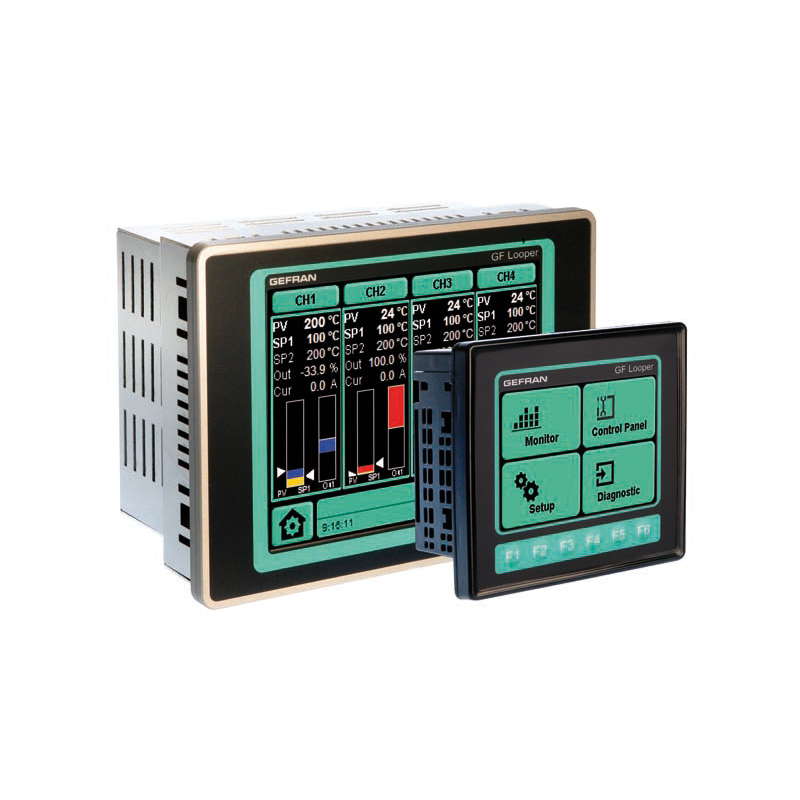
GF_LOOPER PID Controller 16 loops
Overview
GF_LOOPER is an advanced series of multi-runner controllers offered in 16 zone configurations, with complete and easy to use functions for a variety of applications. The operator interface is based on an LCD TFT color touch screen, 3.5” and 5.7”, designed for very easy use.
The work and configuration pages are identified by keys with intuitive icons that give immediate access to selected functions. Predefined password levels, compatible with operator authorization, guarantee controlled access to functions.
The supervision pages offer a complete view of the zones, each with its own PV, SP, output power, and main alarms status levels. All of the control zones can be switched on or off with a single button, and all of the setpoints can be simultaneously changed by the same engineering quantity with two up/down keys.
Selecting the page of a single zone displays the status of all of its parameters, with PV and SP in different colors and a bargraph for intuitive indication of shifts and of the power %.
An icon constantly signals zone status and any fault conditions, such as input interrupt, short circuit, partial or total load interrupt.
If the password level is compatible, the SP, alarm thresholds, AUTOmatico/ MANuale status can be changed and the zone switched on/off from this page. The various pages can be selected directly from the touch screen and, with the 3.5” model, also with 6 mechanical keys with pressed key feedback.
The ability to name and save entire recipes of work parameters for all of the zones provides quick and simple management of device setup for various processes and guarantees error-free operation at all times.
Alarms are displayed on specific screens with clear messages and can be recognized and reset with keys.
Five passwords are provided for different protection levels, ranging from maximum protection (allowing only the active setpoint to be changed) to a level giving access to all parameters.
The data storage page lets you save both work parameters and HW configuration parameters in separate files. Saving the configuration parameters simplifies replacement of an I/O module with Hot Swp functions.
A Trend display page shows the trend of controlled variables, with various colors and the ability to zoom on duration of graphics, with configurable sample time and data saving on USB key in CSV format. For greater flexibility, GF_LOOPER offers a clock/calendar function that switches all of the zones on/off at preset times and days of the week.Different types of control can be selected for each zone, from simple ON/OFF to precise Heat/Cool control with individual double PID.
Selection of optimum control parameters for each zone is made easier by Selftuning and Autotuning functions, activated by keys. GF_LOOPER diagnostics always display any critical process conditions, such as interrupted or short-circuited inputs, and signal total and partial load break with video alarms and physical outputs.
Control of Modbus RTU serial communication signals any communication interrupts.
GF_LOOPER interconnects with other control systems, data storage systems, and supervisors via Ethernet, RS485, and USB ports.
Available protocols: Modbus RTU (Master), Modbus TCP, Profibus DP.
The following functions can be activated for specific applications with hot runners: softstart, control with rapid burst firing for solid state relays and specific diagnostics to detect unwanted variations in power supply and input breaks, with ability to continue to supply average power calculated during the last 5 minutes of operation. Choice of distributed control architecture makes GF_LOOPER a affidable, flexible solution adaptable to equipment of different sizes and with different performance and modularity requirements.
CONTROLLER
Advanced control algorithms provide excellent management of process variables. Various types of control are possible: ON/OFF, P, PI, PID, both heat or cool only and heat+cool. In addition, cooling can be set by specifying the fluid used: air, oil, water. Calculation of the best process parameters is extremely rapid and efficient thanks to the use of sophisticated automatic tuning processes. The use of advanced tuning lets you check the best PID parameters under all conditions.
ALARMS
Two alarm thresholds (minimum and maximum) for each zone. For each alarm, you can select:
- the control variable to be assigned
- the threshold value
- the hysteresis value
- 5 properties (with latch, disable at power-on, deviation/symmetrical, absolute/ relative, direct/inverse).
LBA, HB, SBR alarms can be set; the presence of the alarm is displayed on the screen via LEDs.
Description
- Color graphics screens, TFT, 3.5” and 5.7”, touch screen
- Simplified programming with numeric and alphanumeric keyboards, ticks, direct complete messages and icons
- Distributed control architectures
- Flexible selection of input/output modules in “Geflex” and “Gilogik II” Gefran series
- Preloaded applications from 4 to 16 loops
- Operation with double setpoint preimp state and shared up/down for all setpoints
- Shared pages for supervisions of multiple zones and single pages for each zone
- Bargraph for % output power and deviation
- Active and historic alarms management
- Storage of recipes and configuration parameters on USB key
- Functions include Self-tuning/Auto-tuning, Softstart, sensor diagnostics, solid state actuator diagnostics
- Communication lines on Ethernet, Modbus TCP
- Data acquisition and recording
- On-line trend of variables and setpoints, with selectable channels and zoom
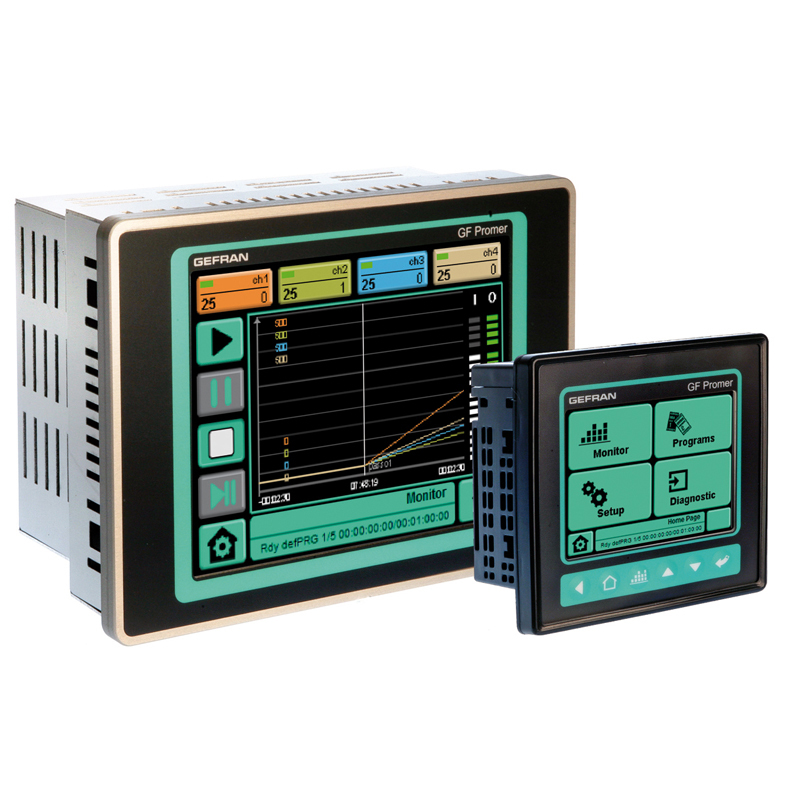
GF_PROMER PID Controller Programmer, 1/16 DIN
Overview
GF_PROMER is a time-variable setpoint programmer, 4-loop controller, graphic trend and bargraph display, all in a single device with data saving functions.
The user interface, based on an LCD TFT colour touch screen (3.5” and 5.7”), is extremely simple to use.
Configuration menus are identified by keys and icons that give immediate access to work program creation pages.
Every program is identifiable with a number and a name, a time base definable in days/hours, hours/min, min/sec, different start and stop strategies. In addition, a number of cyclical repetitions of the program can be set. The programs are in easily scrollable list form and are selected directly on the screen.
The steps are configured the same way with numbers and name, with up to 4 setpoint values for the 4 available loops, and step duration in the time base for the selected program.
Cyclical repetitions of a sequence of contiguous steps can be easily created. To facilitate and speed up programming, there are copy, delete, and add functions for both steps and programs.
When a program has been created, it can immediately be displayed in trend form to intuitively display correctness of the programming.
The program to be run can be selected from the programs list (from screen or digital inputs) and the Monitor page is automatically called up, from which all of the main process data are controlled. The monitor page is divided into two parts and simultaneously shows, in trend form, the trend of controlled variables (at the left of the screen) and of programmed setpoints (on the right).
The data are always based on the real time seen at the center of the page.
The top of the page shows basic data on program name and run state, plus lapsed and remaining time. The monitor page can be adapted to display needs at any time: buttons let you display / hide trend tracks in run-time.
States of enable inputs and event outputs are displayed graphically for each step being run, and the steps are highlighted by name or number on the screen.
Loop engineering scales are independent and each value can be represented on graphs and bar graphs.
The “Hold Back Band” function, independently settable with different values for each step of each loop, checks that the variables trend remains in the defined tolerance “window,” blocking execution of the program if maximum deviation is exceeded.
Bargraph display pages for channels offer immediate data on analog indicators, with different colors to identify heating and cooling phases, and deviation between PV and SP, while a specific bargraph displays output power level.
These pages are also adaptable to the application via buttons, which display zones freely, from 1 to 4.
Under the conditions required, manual variations of setpoint, supplied power, and PID values can be made on the page for each zone.
GF_PROMER provides complete alarms control, with recognition functions, protection of the entire application based on various password levels, and saving of historical data, programs, settings, via USB key.
The choice of “distributed” control architecture makes GF_PROMER affidable, flexible, adaptable to equipment with various performance and modularity requirements.
CONTROLLER
>Advanced control algorithms provide excellent management of process variables.
Various types of control are available: ON/OFF, P, PI, PID both only heat or cool and double-action heat+ cool.
In addition, the cool action can be set via indication of the cooling fluid used: air, oil, water.
Calculation of the most appropriate process parameters is extremely rapid and efficient thanks to the use of sophisticated automatic tuning procedures. Advanced tuning lets you check the best PID parameters under all conditions.
ALARMS
Two alarm setpoints (minimum and maximum) for each zone. For each alarm, you can select:
- the control variable to assign to it
- setpoint value
- hysteresis value
- 5 properties (with latch, disable at switch- on, normal/symmetrical, absolute / deviation, direct/inverse).
You can set LBA, HB, SBR alarms: alarm presence is displayed with an icon and described on the alarms page.
Description
- Colour graphics screens, TFT, 3.5” and 5.7” touch screen
- Simplified programming with complete, direct messages and icons
- Distributed control architectures
- Flexibility in selection of Gefran “Geflex” and “GILOGIK II” series input/output modules
- Up to 300 steps in 100 programs
- Free configuration of step sequence repetitions and entire programs
- Up to 4 control loops with setpoint profile
- 16 programmable enable inputs, 16 programmable event outputs for each step
- Configuration of logical and combined or timed automation sequence
- On-line trend for variables and setpoints, with selectable channels and zoom
- Programmed setpoint profile trend
- PV, SP and Power% bargraph with selectable channels
- Active alarms control
- Historic data and parameter saving on USB key
- Ability to add auxiliary I/O for program control, enable inputs, event outputs
- Functions: Self-tuning / Auto-tuning, Soft-start, sensor diagnostics, solid state actuator diagnostics
- Communications lines: Ethernet, Modbus TCP
- USB port for SW updates